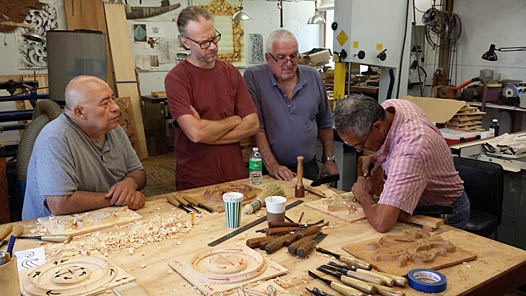
Before you start carving your walking stick, you will want to know which woods work best. Also, you will want to be familiar with the different techniques of whittling. David Allen used these techniques to carve his walking sticks. You can also find famous quotes about walking sticks, and how to carve them. Here are some tips to help make the perfect walking sticks. So, read on to learn more! You can now carve a walkingstick that will be functional and unique!
Woods that can be used for carving a walkingstick
Finding a straight blank to carve is the most challenging part of the process. There may be a few branches that are too bent to be of use, but it is worth searching until you find one. A straight branch can be harvested during winter when the sap is moving from the roots to the branches. This will make the wood more stable, and less likely to split. If you don't have the time to wait for spring, you can still harvest the wood while it is still green.
You can use a variety of wood species to carve a walking stick. North American Chestnut is a solid wood. Its density makes it ideal for making walking sticks and other similar tools. This species' wood grain is either slightly open or partially closed. This wood grain makes a strong walking tool that is solid and smooth. It is also very attractive and is used extensively in carving. You can carve some species with the bark still in place.
Techniques for making a walking stick
A few simple techniques are required to carve a walking sticks. First, you should choose a piece of wood with a unique texture. Some woods have distinctive bark marks and colors, and other woods have natural swirls. You may want to enhance these features by using lacquer or paint. You may also want to carve the shaft of wood to enhance its beauty. Finally, ensure you choose straight sticks that are free of branch shoots and tough spikes.
This book will teach you about different wood types and carving styles. The most popular designs are snakes or lions. Other than snakes, it is possible to carve realistic figures, such as fish, deer, and eagles. These artists are often regarded as God-given. This book is both for the experienced and the novice carver.
David Allen uses these tools when carving a walkingstick
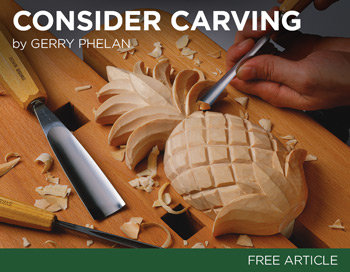
David Allen started making toys when he was young. He used a pocketknife from his childhood to create them. He had to hide it from his family, as he was considered too young to play with a knife. His creations included toys, like slingshots, as well as utilitarian tools like shoeshine cases. Allen began to carve walking sticks at the age of 15 after becoming disabled. Allen used a pocketknife as well as a chisel for carving the wood.
Allen devised his designs on his own, looking at the roots of saplings to decide what to carve. Allen believed that design must be "seeable" before carving can begin. This process reminded him of the work of many African American artists. Allen had many visions and dreams of the design he wanted. He was able create a stick which would invoke the emotions and feelings in his community.
Famous quotes regarding carving a walking stick
Carving walking sticks is a complex task that requires a well-prepared blank. The hardest part of the project is finding a straight blank. While there are many places to source your stick from, it's important that you persevere until you find one that is straight. Although it may look bent beyond practical utility, you can keep looking until you find one. It is best to cut your stick during winter sap flow from the tree's branches down to the root. Sap makes wood more flexible and less likely to break.
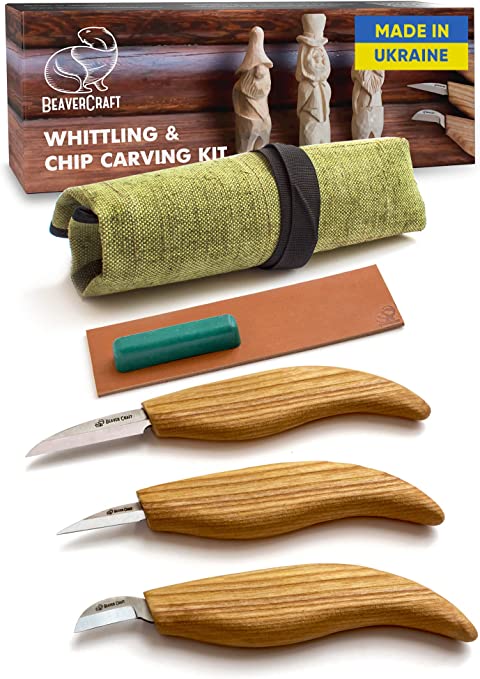
Consider the wood's texture when choosing wood. Every piece of wood is unique and has its own texture. The lacquer will make these natural swirls even more beautiful. To ensure a smooth finish, it is important to choose a wood shaft free of branch shoots or tough spikes. This will simplify the whole process. Regardless of what material you choose, you should carefully consider the type of finishing you'll use.
FAQ
Where can I purchase woodworking supplies
There are plenty of places where you can find everything you need to start out. You could also visit hardware stores in your area or shop online at Amazon.com.
You can also check garage sales and flea markets for old furniture and other materials you can reuse.
What kind wood should I use for my project?
Woodworking is a popular job that involves oak, pine and maple. Each wood variety has distinct characteristics that influence the final product's look and feel. Oak is a darker wood and tends to be more durable than other types. Birch is light and soft, while mahogany can be heavier and more dense. You can also choose between solid wood and veneers. Veneers are thin sheets of wood that are glued together to form a single layer.
What material would your recommendation be to learn woodworking?
Start with softwood like pine, poplar and ash. You will feel more comfortable with these softwoods, so you can move onto hardwood.
How much should a skilled woodworker earn per hour?
The hourly rate for a professional Woodworker will vary depending on many variables, such as experience, skill level and availability.
An average hourly rate for skilled woodworkers ranges between $20-$50.
A less experienced woodworker may charge as little as $10 an hour.
Statistics
- In 2014, there were just over 237,000 jobs for all woodworkers, with other wood product manufacturing employing 23 percent; wood kitchen cabinets and countertop manufacturing employing 21 percent. (theartcareerproject.com)
- Average lumber prices rose about 600 percent between April 2020 and May 2021. (familyhandyman.com)
- If your lumber isn't as dry as you would like when you purchase it (over 22% in Glen Huey's opinion…probably over 10-15% in my opinion), then it's a good idea to let it acclimate to your workshop for a couple of weeks. (woodandshop.com)
- The best-paid 10 percent make $76,000, while the lowest-paid 10 percent make $34,000. (zippia.com)
External Links
How To
How to stain wood
Staining wood is the process of applying chemicals to the wood's exterior, which alters its color. This chemical reaction causes the wood to change from white to brownish red. While oak is the most widely used type of wood for staining purposes, other types of wood are also available.
There are many ways to stain wood surfaces. Some methods involve mixing the stain with a solvent (such as turpentine) and then brushing or spraying the mixture onto the wood. Another method involves applying a solution of water to the wood. You can mix stains into varnishes or paints to make them part of your finish coat.
Preparing your wood for staining is the first thing to do. The wood must be thoroughly cleaned to remove all grease and dirt. Sanding can smoothen out scratches and uneven spots. You must then decide on the type of stain that you wish to use. There are two main types of stain: non-penetrating and penetrating. Penetrating and non-penetrating wood stains penetrate deeper than other types, making them perfect for dark colors like mahogany. Non-penetrating oils work best when used with light colors, like maple.
After choosing the type and application method you prefer, gather your tools. You can use a paintbrush to apply stains. This allows you spread the liquid evenly over the surface. After you're done painting, make sure to have some rags handy to remove any excess stain. If you plan to mix the stain yourself, make sure you have enough containers available to hold the different components of the mixture.
Once you have prepared all your materials, it is time to clean the areas where you will stain the wood. Use soap and warm water to remove dust and grime. Use a dampened rag and clean water to wipe the furniture. Be sure to get rid of all loose material, especially if staining is planned for darker wood.
Apply the stain. Next, apply the stain to the furniture by starting at one end. Slowly and carefully move along the grain of wood, slowly but steadily, until you reach the other end. Make sure that the stain does not drip off the edge of the wood. Allow the stain to dry completely before you move on to the next step.
A coat of clear polyurethane sealing agent is applied to protect the paint. Apply three coats of polyurethane sealer. Allow the third coat to dry overnight before sanding the final coat.