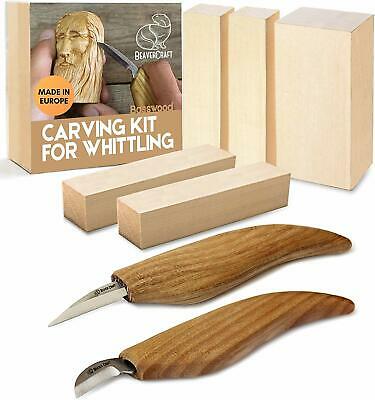
Before you start carving your walking stick, you will want to know which woods work best. You will also want to know about various techniques for whittling and what David Allen uses to carve his walking sticks. A few famous quotes about walking sticks are also available. Here are some tips that can help you carve the perfect walking stick. Read on to learn more. You can now create a walking stick that is unique and functional!
Woods that can be used for carving a walkingstick
The hardest part of carving is finding the right blank. There may be a few branches that are too bent to be of use, but it is worth searching until you find one. A straight branch can be harvested during winter when the sap is moving from the roots to the branches. This will make the wood more stable, and less likely to split. You can harvest the wood as soon as the tree is green, even if it is too late for the spring.
You can use a variety of wood species to carve a walking stick. North American Chestnut is a solid wood. Because it is dense, it can be used to make walking sticks and other similar tools. The wood grain in this species is often open or slightly closed. It is a solid walking stick, which feels smooth and solid. It is also extremely attractive and is often used in carve. Some species can be carved without the bark.
Techniques for whittling a walking stick
A few simple techniques are required to carve a walking sticks. First, choose a piece with a unique texture. Some woods display distinctive bark marks or colors, while others show natural swirls. You may want to enhance these features by using lacquer or paint. To make it look more appealing, you could also carve the wood shaft. Finally, ensure you choose straight sticks that are free of branch shoots and tough spikes.
This book will tell you all about wood types and different carving styles. Most common are snakes and Lions. Other than snakes, it is possible to carve realistic figures, such as fish, deer, and eagles. Many people consider the talents of these artists divine. This book is suitable for advanced and novice carvers.
David Allen uses the following tools for carving a walkingstick
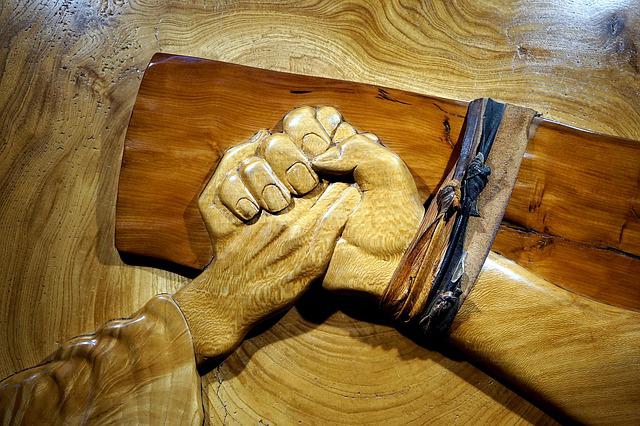
David Allen began to make toys as a child with a pocketknife that he found under his home. Because he was too young for a knife to be used, he had the knife hidden from his family. His creations included toys, like slingshots, as well as utilitarian tools like shoeshine cases. At the age of 15, Allen became disabled and began carving walking sticks. Allen worked with a pocketknife, a chisel and a chisel to carve the wood.
Allen created his designs alone, digging around the roots saplings to find out what to carve. He believed that the design should be "seeable" before it could ever be carved. This process was similar to that of many African-American artists. Allen often had visions and dreams for the design he wanted. He was able create a stick which would invoke the emotions and feelings in his community.
Famous quotes regarding carving a walking stick
Carving a walking stick requires complex skills and a solid blank. This is the most challenging part of the whole project. While there are many places to source your stick from, it's important that you persevere until you find one that is straight. You may find it bent beyond practical use. Keep searching until you find it. You should try to cut your stick at the time sap flows from the tree's roots to its branches. The sap makes the wood softer and less likely that it will split.

Consider the wood's texture when choosing wood. Each piece of wood may have unique textures and colors. The natural swirls can be enhanced with a coat lacquer. To ensure a smooth finish, it is important to choose a wood shaft free of branch shoots or tough spikes. This will make the process much easier. No matter what material you choose to use, it is important that you consider the type and finish you will use.
FAQ
What is the difference in plywood and particleboard?
Plywood consists of layers made from wood and pressed together by pressure. Plywood comes in several thicknesses and is commonly used for cabinets and flooring. Particle board can be made from sawdust, resin, and then compressed to make large blocks. This board is commonly used in home improvement projects. Both types of boards can be easily cut and are durable.
How much should a hobbyist invest to get started?
If you're looking to start your own woodworking business, you'll probably need some capital to buy the necessary tools and supplies. Start by getting a small circular saw saw, drill press or circular saw. These items aren’t too expensive so you won’t have to break the bank.
Is it hard to start my own woodworking business?
It is difficult to start your own woodworking company. You will need to adhere to many legal requirements. You don't have to go through all that hassle of setting it up. Many people choose to join existing businesses. This will allow you to avoid paying membership fees and taxes.
Where can I find free woodworking plans?
To find free woodworking plans, you don't have to buy any magazines or books. You only need to Google search. You can search Google for "free woodworking" and hundreds of websites will appear allowing you to download plans.
What is the difference in a hobbyist and professional woodworker?
Hobbyists enjoy making things out of wood, whereas professionals focus more on the quality of their work. Hobbyists are proud of their creations and will often share them with family members and friends. Professionals will spend hours researching designs and then begin to create a project. They will meticulously plan every detail of their work from choosing the right materials to finishing it.
Statistics
- In 2014, there were just over 237,000 jobs for all woodworkers, with other wood product manufacturing employing 23 percent; wood kitchen cabinets and countertop manufacturing employing 21 percent. (theartcareerproject.com)
- Woodworkers on the lower end of that spectrum, the bottom 10% to be exact, make roughly $24,000 a year, while the top 10% makes $108,000. (zippia.com)
- If your lumber isn't as dry as you would like when you purchase it (over 22% in Glen Huey's opinion…probably over 10-15% in my opinion), then it's a good idea to let it acclimate to your workshop for a couple of weeks. (woodandshop.com)
- Most woodworkers agree that lumber moisture needs to be under 10% for building furniture. (woodandshop.com)
External Links
How To
How to stain wood
Staining wood can be described as a process where chemicals are applied to the wood surface. This causes the wood to take on a new color. The wood will turn from white to brownish-red due to the chemical reaction. The most common type of wood used for staining is oak, although many other types of wood can be stained.
There are several ways to apply stains to wood surfaces. You can mix the stain with a solvent, such as turpentine, and spray it onto the wood. You can also apply a solution containing water and dye directly to the wooden surface. You can also mix stains with varnishes or paints so that they become part the finish coating.
Preparing your wood for staining is the first thing to do. Clean the wood to get rid of any grease, dirt or other substances that might be detrimental to the stain's application. Sanding smoothens any scratches or rough spots. The next step is to choose the stain type you want. There are two main kinds of stains available: non-penetrating stains and penetrating. Penetrating stains penetrate deeper than non-penetrating stains, which makes them great for dark colors like mahogany. Light colors such as maple work well with non-penetrating stain.
You will need to decide on the type of stain you want to use, and then prepare your tools. Because you can spread the stain evenly with a paintbrush, it is ideal for applying them. After you're done painting, make sure to have some rags handy to remove any excess stain. If you plan on mixing the stain yourself make sure that you have enough containers to hold the different components.
After you have prepared the materials, you can clean the area where you want to stain the wood. You can remove grime and dirt with warm water and soap. Wipe down all furniture pieces with a dampened cloth and clean water. Be sure to get rid of all loose material, especially if staining is planned for darker wood.
The stain should be applied next. Apply the stain by brushing or spraying it onto one side of the furniture. Work slowly and carefully, moving back and forth along the grain of the wood until you reach the opposite end. Make sure that the stain does not drip off the edge of the wood. Let the stain dry completely before proceeding with the next steps.
Apply a clear polyurethane sealant to protect the painted surface. Three coats of polyurethane sealing agent are required. Allow the third coat to dry overnight before sanding the final coat.