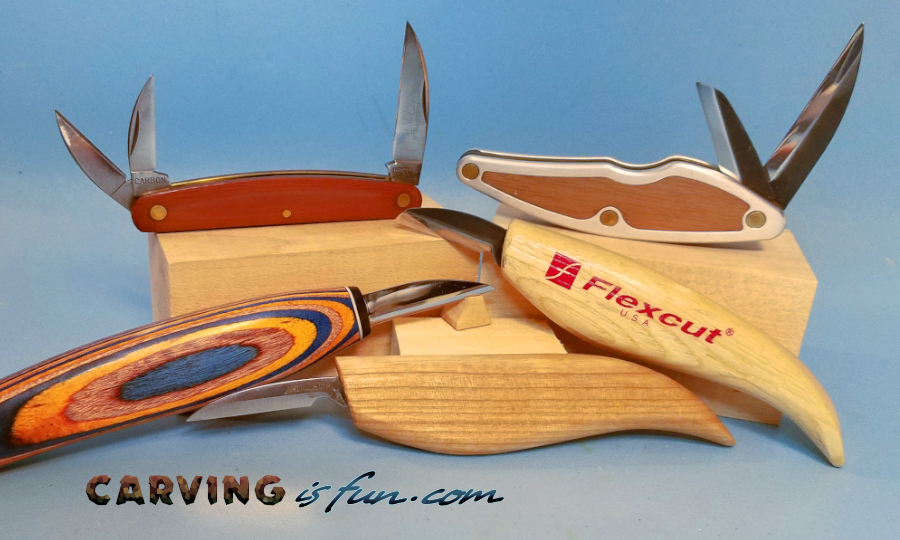
Two different methods are woodcarving and whistling. In both of them, wood is removed from a larger piece and changed into a different shape. A spoon for the kitchen can be transformed into a carving measuring 10 feet. But the key difference is that both require you to take the wood material out of the original piece. Wood carving is different from whittling. It doesn't require clamping or glueing, joinery, or any other methods.
Woods to carve
Many woods are suitable for carving. Green, moist, dried, rotten, or fresh are the best. You will be able to carve more easily if you select straight grain wood with minimal knots. For carving, wood with large knots or side branches is not recommended. Ask the tree surgeons or park wardens for help in choosing the right wood. They can guide you in the correct direction.
One of the easiest woods to carve is pine, which is easily available in the US. It is soft and can hold its details well, despite having knots. Pine can last a lifetime if it is properly maintained. In Norway, for example, the load-bearing orepine stave churches that have survived over eight hundred years have been preserved. If you are just starting out, this is a good choice.
Use of tools
You must first draw your design onto the wood before you begin wood carving. For straight cuts, a hand saw is a good choice. But fine details can be carved with a chisel or a chisel. A gouge is great for rough shaping, as it can quickly remove large quantities of material. It can also be used to smoothen rough areas.
There are many different types of knives. For finer detail work, bench knives may be used. These can cut into wood and can also be used to remove larger parts in detail work. While a chisel can be used to cut through thicker wood, bench knives are also useful for making delicate cuts. The best tools are essential for a successful project.
Techniques

Sharp knives are essential for smooth, controlled cuts, which are the backbone of good whittling and wood carving. A dull knife causes frustration, blisters, and tired hands. A sharp knife makes it easy to focus and more enjoyable. Whittling enthusiasts can enjoy deep thought and breathing as they carve intricate details and designs with the sharp blade.
There will be mistakes, just like any craft. You will make mistakes, but that is all part and parcel of the craft. Some of your first creations might be unsymmetrical or cut against the grain. It is possible to be too eager to carve the nose, and end up with nothing. Learn from your mistakes. Wood carving can be a rewarding hobby that can inspire and encourage you to create new designs.
The most popular of these two wood-carving methods is whittling. It is the oldest form wood-carving method and requires a pocketknife/straight knife. It is easier than carving hardwoods. Whittling is characterized by knife marks. Wood carvings don't require sanding and are easy to make with no costly tools.
Getting started
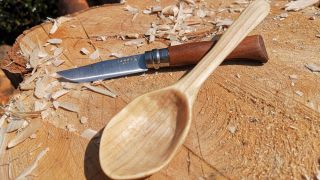
The first step to getting started with wood carving and whittlinng is to select a piece of wood. Although you have the option to use many different wood types, beginners should start with basswood. Avoid wood with holes or knots. Smooth branches are easier to carve. You can purchase beginner-level woods at craft shops. The following tips can help you get started with wood carving.
Make sure you have the right tool. Sharpening and durability are important features of the whittling tool. For the first few cuts, use a high-quality knife. A sharp blade ensures better cuts. A dull blade tends to glance off the wood and head toward the hand, while it can cut human flesh. When carving, these are the most important tips. This will make the whole process easier. Continue reading to find out more about the art wood carving and whittling.
FAQ
Can you teach yourself woodworking?
Doing is the best way to learn any subject. Woodworking is an intricate art form that requires practice, skill, patience, and experience. Mastering any craft takes time.
The best way to learn how to do something is actually to do it. Start small, and work your way up from there.
What is the minimum amount I will need to start?
Because every project is unique, there aren't exact numbers. But if you want to get an idea of how much money you'll need, consider these factors:
-
Material cost
-
Tools and equipment
-
Time spent working on this project
-
Hourly rate
-
How much profit do you expect to earn
-
Whether you plan to hire help
It's a good idea for beginners to start with small projects like frames and boxes. As you gain experience, more difficult projects will become possible.
Do I have to refinish my furniture?
Yes! You don't have to hire a professional to refinish furniture. There are many ways you can do it yourself. Here are a few suggestions:
Sandpaper can be used to remove stains and scratches. Next, wipe the surface clean with a damp cloth.
Apply clear polyurethane finish. Allow to dry thoroughly before moving furniture.
Paint furniture with acrylic paint.
Instead of using paint, stain is a better choice. Furniture will look richer with the stain.
Use shellac wax. You can protect your wood with wax and give it shine.
Where do I get my woodworking supplies?
There are many places that you can find all the information you need. You can visit your local hardware stores, or you can look online at sites like Amazon.com.
You might also consider flea markets and garage sale for any old furniture or other materials you could reuse.
Can this be a way to make money?
Yes! In fact, most woodworkers already have it. According to the U.S. Bureau of Labor Statistics' (BLS), in May 2012 the median annual wage of woodworkers was $34,000 This is much higher than the national median of $31,000 per annum.
Statistics
- The U.S. Bureau of Labor Statistics (BLS) estimates that the number of jobs for woodworkers will decline by 4% between 2019 and 2029. (indeed.com)
- Most woodworkers agree that lumber moisture needs to be under 10% for building furniture. (woodandshop.com)
- If your lumber isn't as dry as you would like when you purchase it (over 22% in Glen Huey's opinion…probably over 10-15% in my opinion), then it's a good idea to let it acclimate to your workshop for a couple of weeks. (woodandshop.com)
- Woodworkers on the lower end of that spectrum, the bottom 10% to be exact, make roughly $24,000 a year, while the top 10% makes $108,000. (zippia.com)
External Links
How To
How to make wood joints
This tutorial will show you how to join two pieces of wood together. We'll use the "pocket hole joint," which means we drill holes in the wood and then glue them together. If your wood has a straight grain, smooth surface, you can use this method. You may want to consider other methods, such as dowel joining. These are the steps
-
Drill Pocket Hole Joints. Measure and mark the location where you would like to place the pocket hole joint. Then drill 3/4 inch deep holes into the ends of each piece of wood using a jig saw or handheld drilling machine.
-
Sand Smooth. You can sand the edges of the wood to ensure that it doesn't split.
-
Glue Together Apply glue to both ends of the wood. Allow it to cool for at least 5 minutes before you attach the pieces.
-
Clamp the Pieces Together. Once the glue has dried, clamp the pieces together so they are flush.
-
Trim Joinery. Trimming the joinery after glue has completely dried.
Be sure to leave enough space between each piece so that they can be turned inside-out.