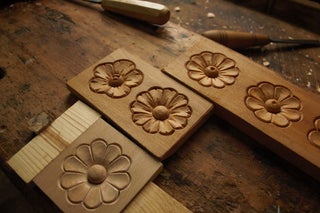
Select a piece of wood to begin carving a face out of wood. Make the necessary cuts. The expert will guide you through the process using a step-by, video tutorial. This will allow you to create a more realistic face by making the cuts in the wood. To create a realistic face, the progression of the noses is key. In addition to the face outline, you may also choose colored dyes and shellac to add a realistic finish.
Hardwoods
Before carving a face out of wood, it is important to consider what type of wood you will be using. Hardwoods can be described as a group of trees with large leaves that can thrive in many climate zones. Hardwoods are ideal for many purposes, such as furniture building and furniture making, due to their large range in density, strength, and appearance. Hardwoods can be more cost-effective than softwoods but are durable and fire-resistant.
If you're new to wood carving, you may want to consider using softwood, such as basswood or butternut. These woods are easy to work with, and are great for beginners. You should keep in mind that soft woods will not have the same quality or finish as hardwoods. Before you decide on a type of wood, try out different types.
Softwoods
When carving a face from wood, the first step is to choose the right softwood. Softwoods tend to be more difficult to carve and will often have many knots. They are also more likely to crack if you use big strokes. The smallest pieces of wood will be cut by a beginner carver, which reduces the amount of detail. While this isn't a major issue, it is something to be aware of.
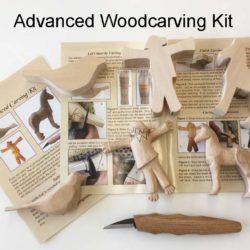
Some hardwoods are more difficult to work with than others. Aspen, butternut, basswood, and other hardwoods are some of my favorite to work. A steeper bevel is better for this reason. Softwoods are also easier to work with than hardwoods, so you can carve them either along or across the grain. The wood that you use for carving will determine the quality of the finished product.
Colored dyes
To create a vibrant, detailed finish on a wood carving, try using colored dyes. These dyes come in many colors, and you can mix them with alcohol or water to make your own unique color. For lighter woods, you can use colored dyes mixed with shellac. Use denatured alcohol to clean your brushes after you have applied the dyes. You can also use paste wax. Excessive glossiness can distract you from your work. Use 0000 Steel Wool to remove any excessive glossiness.
Wood dyes come in many varieties and are easy to use. Wood dyes are compatible all topcoats, and they are easy to use. They can solve common finishing problems. They are easy to mix and use because they come in many primary colors. You can also mix and match them to your liking. They can be mixed to create new colors.
Shellac
Shellac should be available before you apply it to your wood carvings. It is possible to buy a container of shellac but using a brush is the best method to apply it. A two-pound cut should suffice. This is because it will grow slowly and will reduce the brush marks. A thicker cut is better than a thin one because shellac can be very water-thin. You can make your own pads from cotton lumps the size of golf balls and lint-free cloth. After that, dip the tip end of your brush in the shellac.
Use shellac to add color and highlight grain. Shellac can be mixed with different colors to create custom blends. You can even darken the shade by applying extra coats of the lac. Shellac is not like other wood finishes. It won't become yellowed or cloudy over time. It will also last longer, so you can make more faces. This can be done with any type or wood carving project.
Gouges
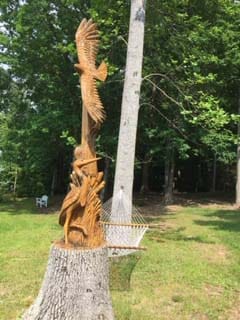
There are many different sizes and shapes available for gouges. The most common types of gouges are the straight and palm gouges. Straight gouges are designed to be held by hand while palm gouges have shorter shafts and handles. Hand held carving is easier with the shorter handles. These palm gouges can also be called veiners. They are perfect for carving faces into wood. These are some important things to remember before you begin carving.
The first step is to know how you can choose the right gouge. You need a gouge that can carve a shallow groove. Make sure you buy a tool with a sharp edge and a small sweep. Gouges are often categorized according to their size. A 3/10 gouge will make the same-size cut as a 5/10 gouge. The scoop between the edges will get deeper and the sweep will become more curled as the first number goes up. A small-sized gouge will be capable of carving a shallow profile.
FAQ
How much money does a hobbyist have to put into getting started?
A lot of capital is required to purchase the necessary supplies and tools if you want to start your own woodworking shop. You can start by purchasing a small table saw and drill press as well as a circular saw, circular saw, jigsaw and sanding machines. These items aren't very expensive, so you won't break the bank.
What tools work best for me?
It is important to consider your needs and preferences when shopping for tools. Do you prefer metal or plastic handles What size screws or nails do you prefer? Do you prefer hand tools over power tools?
How often should I get new supplies?
You may have to replace certain tools. You'll need to sharpen your hand tools regularly if you use them. For power tools, replacement parts will be required frequently. You can spread your purchases over a number of months to avoid spending too much.
Statistics
- Overall employment of woodworkers is projected to grow 8 percent from 2020 to 2030, about as fast as the average for all occupations. (bls.gov)
- If your lumber isn't as dry as you would like when you purchase it (over 22% in Glen Huey's opinion…probably over 10-15% in my opinion), then it's a good idea to let it acclimate to your workshop for a couple of weeks. (woodandshop.com)
- In 2014, there were just over 237,000 jobs for all woodworkers, with other wood product manufacturing employing 23 percent; wood kitchen cabinets and countertop manufacturing employing 21 percent. (theartcareerproject.com)
- The U.S. Bureau of Labor Statistics (BLS) estimates that the number of jobs for woodworkers will decline by 4% between 2019 and 2029. (indeed.com)
External Links
How To
Here are some tips on how to drive nails in wood
First, choose the right size and type of tool to drive a nail through wood. Claw hammers include mallets, claw hammers (sledgehammers), mallets, ball-peen hammers, hatchets, and mallets. Each type of hammer has its pros and cons. A claw hammer is best for hitting nails or hard objects. However, it can be difficult to pinpoint exactly where the blow will land. Although a sledgehammer can be used to hit large areas quickly, it is too heavy to be useful for small tasks.
After selecting the right hammer, you will need to place your hand flat against one side of the head. The handle should rest comfortably in your hands. Grip the handle firmly, but don't squeeze it so tightly that you hurt yourself. Hold the hammer straight up, keeping your wrist relaxed. Next, swing the hammer toward the ground and aim for the nail's center. The impact of the hammer hitting the nail should be felt. Practice swinging your hammer on a block of wooden until you feel comfortable.
Hold the hammer near your body until you're ready for the nail to be driven. You will need to position the nail so it is parallel to the wood. Keep your eyes focused directly on the tip of the nail. Swing the hammer forward, then follow through with the motion of the hammerhead. Repeat this action several times, gradually increasing the speed of the swing. After mastering the technique, you can add power to your swings. Hold the hammer high above your shoulders and pull it down. This will help you put more energy behind each of your moves.
Once you've nailed the first hole, remove the hammer from the nail. To pull out the remaining nails, use a screwdriver or pry bar. Keep the nail heads parallel to the board's surfaces in order to avoid splitting wood.