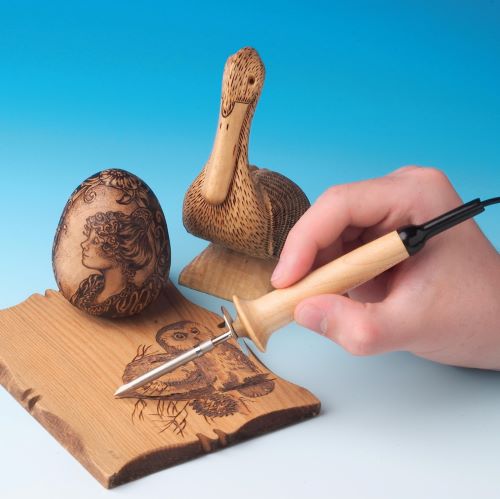
Many materials can be used to create wood burning art. If you are looking for a bright color without any visible grain, then basswood might be a good option. Unfortunately, this wood is often very expensive and hard to find in the size you need. Birchwood is another popular wood that is light in color and has a fine texture.
Preparing wood to be used in pyrography
Preparing the wood for pyrography is the first step. Dark wood won't display the art as well as wood with a prominent grain pattern. For pyrography, you should avoid using resinous or uneven wood. Make sure to clean the wood before you start burning it. After you've prepared the wood for burning, it is ready to go!
Although shellac can be used for pyrography projects sealing, it is temporary. Shellac discolors wood when exposed to heat, and should not be used on cutting boards or coasters. Paste wax is an alternative to shellac. Paste wax gives wood a smooth, natural sheen when it is applied. It is easy to apply, and it looks natural.
Designing wood
If you want to add design to your wood burning art, start by creating a light sketch of the design that you'd like to create. This can be done with a pencil or eraser, ruler, ruler, compass, or printed templates. Premade stencils are particularly useful. For beginners, you can purchase complete wood burning sets. Here are some wood-burning design ideas to help you get started.
You can also paint on the burned art. You can use either a pointed pen, or a flat pencil. But be careful not to burn too much or you might end up with holes. To add shading to wood burning art, you can also paint. When you're finished, you can also apply color to it. After the wood has cooled down, you can add shading.
Creating Lichtenberg burns
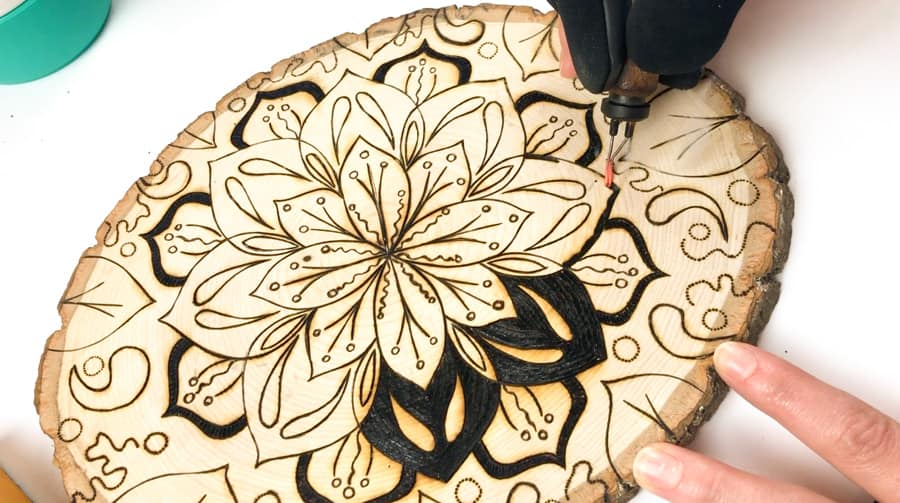
The art of creating Lichtenberg burns has a lot potential. Using a microwave transformer and a high voltage, you can create branching electrical discharges. Lichtenberg first discovered Lichtenberg figures in 1777. Fractal wood burning has made Lichtenberg burns an increasingly popular form of art. Here are some tips to make these figures.
Before you begin, you'll need some safety equipment. You will often use high-voltage Transformers to power appliances and neon signs. They are more at risk for electrocution because they are often unprotected and expose to live electrical wiring. When using a Lichtenberg device, gloves are recommended. Also, you should wear a pair of rubber gloves. If you use gloves, make sure you only touch one hand at a time, holding the other hand behind your back. Your heart rate will not be stopped by an energized electrode, but your hand might still be shocked. A second thing you should remember is to always have someone there to assist you with a Lichtenberg unit. If you are electrocuted, this second person will turn off the electricity.
You will first need a power source. A Lichtenberg device requires a high-voltage electrical source. Burning wood can only be done with an electrical current of at least 2,000 volts. This is why many woodworking organizations prohibit the use of this method. Safety is the main concern, regardless of whether you are creating a Lichtenberg figure. Protective clothing and gloves are essential when working with electric current. Before you contact the outlet, make sure to double-check it.
Using a stencil
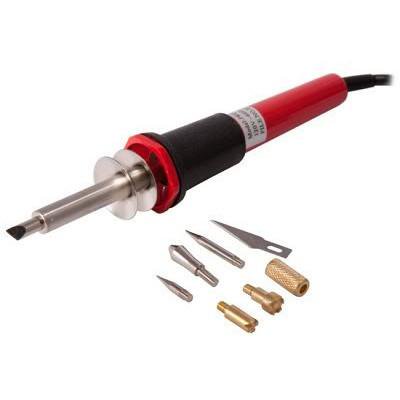
A stencil is a great tool for creating intricate wood-burning designs. You can trace a design on a graphite sheet, and then transfer it onto the wood. The stencil will guide your eyes and hands but you are free to design the final product. While it is possible to use a pencil to draw a pattern, holding the stencil and the wood at the same time can result in burns.
You must first sand the wood where you will be burning the image. Once the wood has been sanded you can begin designing. You will need to apply some pressure to transfer graphite onto the wood to make sure that the design is clear. You will need to remove the trace paper once you're done.
FAQ
How can I keep my shop organized?
The first step toward keeping your workshop clean and organized is to set aside a designated area for storing tools. To keep your tools sharp and ready for work, keep them clean of dust and debris. You can hang tools and accessories with pegboard hooks.
How much do hobbyists need to invest in starting a business?
To start your own woodworking company, you will likely need capital to purchase the necessary tools and other supplies. You can start by purchasing a small table saw and drill press as well as a circular saw, circular saw, jigsaw and sanding machines. These items aren't very expensive, so you won't break the bank.
How long does it take you to finish a piece?
It depends on what size piece of furniture you have. Boxes and picture frames are small projects that can be completed in one day. Larger projects, like desks or dining tables require several days. It takes time and effort to properly stain the wood.
This is a job that I can make a living from.
Yes! Many woodworkers are already doing so. According to U.S. Bureau of Labor Statistics (BLS), woodworkers earned a median annual salary of $34,000 in May 2012. This is much higher than the national median of $31,000 per annum.
Where can I find my woodworking tools?
You can find everything you need in many places. You can visit your local hardware stores, or you can look online at sites like Amazon.com.
You might also consider flea markets and garage sale for any old furniture or other materials you could reuse.
Statistics
- Average lumber prices rose about 600 percent between April 2020 and May 2021. (familyhandyman.com)
- The best-paid 10 percent make $76,000, while the lowest-paid 10 percent make $34,000. (zippia.com)
- If your lumber isn't as dry as you would like when you purchase it (over 22% in Glen Huey's opinion…probably over 10-15% in my opinion), then it's a good idea to let it acclimate to your workshop for a couple of weeks. (woodandshop.com)
- The U.S. Bureau of Labor Statistics (BLS) estimates that the number of jobs for woodworkers will decline by 4% between 2019 and 2029. (indeed.com)
External Links
How To
How to make wood joints
This tutorial will show how to join 2 pieces of wood together. We'll use the "pocket hole joint," which means we drill holes in the wood and then glue them together. If your wood has a straight grain, smooth surface, you can use this method. You might consider dowel joinery if your wood isn’t straight or flat. These are the steps
-
Drill Pocket Hole Joints. Measure and mark the location where you would like to place the pocket hole joint. Next, drill 3/4 inch holes in each end of each piece using a handheld drilling machine or jigsaw.
-
Sand Smooth. Sanding the edges of the wood will help to prevent the joint from splitting later.
-
Glue Together. Apply glue to both sides of the wood. Allow it to sit for approximately 5 minutes before you clamp the pieces together.
-
Fix the Pieces together. After the glue has dried thoroughly, secure the pieces so that they are flush.
-
Trim Joinery. After the glue dries completely, trim off any excess wood around the joint.
Be sure to leave enough space between each piece so that they can be turned inside-out.